Получение карбида кремния
Наибольшее количество природного происхождения карбида кремния содержится в космическом пространстве: на пылевых облаках, окружающих звезды, в метеоритах. На Земле этот материал присутствует только на месторождениях кимберлита или корунда, что усложняет процесс его добычи в промышленных масштабах. По этой причине карборунд, используемый в современной индустриальных сферах и бытовых условиях, является искусственным. Самым распространенным способом получения этого химического соединения является нагревание двуокиси кремния углеродом в специализированных печах, работающих на электричестве. Вещество нагревается до температуры 1800-2300 °C.Источниками кремния являются кварцевый песок, очищенный от примесей, и антрацит. Для улучшения газопроницаемости материала используются опилки из древесины. Цвет синтетического карборунда изменяется при помощи добавления хлорида натрия (поваренной соли). Увеличение плотности материала производится при помощи прессования. После этих процессов структурные частицы меняют свое местоположения, что приводит к деформации твердого раствора.
Также данное вещество получают при помощи следующих методов:
- Сублимация. Это технология предоставляет выращивать зерна карбида кремния природных материалов. Рост кристаллов осуществляется в графитовых тиглях из газовой фазы. Получить карборунд при помощи этой технологии можно из инертных газов, нагретых до температуры 2600 °C.
- Эпитаксия. Этот способ используется для получения твердых растворов карбида кремния. В нем используется водород, предварительно очищенный от примесей при помощи диффузионных методов. Химический элемент вступает в реакцию со свободным углеродом, что приводит к образованию полупроводниковых пленок.
- Синтез. Сырьем для получения карборунда является графит, измельченный до порошкообразного состояния. Также для получения необходимого материала можно использовать сажу с размером частиц не более 20 мкм. Синтез химических веществ происходит в твердой фазе, что обусловлено большим расстоянием между атомами углерода и кремния.
- Приготовление шихты. Для этого метода требуются компоненты, содержащие большое количество углерода и кремния. В качестве сырья могут использоваться нанопорошки, углеводы или многоатомные спирты. Приготовление шихты осуществляется в деионизованной воде в течение 5,5 часов. Материал нагревается ступенчато до температуры 1650 °С.
Для промышленных нужд чаще всего изготавливают карбиды зеленого и черного цветов. Особенности их химического состава определены в ГОСТ 26327-84. В нем указаны 4 марки карбида кремния: 53С, 54С, 63С и 64С.
История
Любопытна история камня. Здесь не обошлось без научного заблуждения, рождённого самоуверенностью.
Второе название камня — муассанит. Оно присвоено в честь французского химика XX века — Фердинанда Анри Муассана, прославившегося получением фтора, за что и получил Нобелевскую премию.
Но ещё до этого знаменательного события Муассан изучал минералы в Каньоне Смерти, который образовался в Аризоне из-за падения метеорита.
Вооружившись пилой честолюбивый и активный учёный, начал разделывать камни в поисках сенсации. Кто ищет — тот найдёт. В одном из булыжников мелькнул SiC. Муассан не стал откладывать дело в долгий ящик и продемонстрировал находку учёному миру. Напомним, что он был известным учёным и имел вес в научных кругах. Это и сыграло роль. Долго разбираться не стали и назвали находку муассанитом, закрепив за Фердинандом Анри звание первооткрывателя.
Однако и мировое научное сообщество, и Муассан обманулись. Соединение SiC было получено Э. Г. Ачесоном лабораторным путём задолго до открытия муассанита. Это был простой и действенный способ, который Ачесон запатентовал. Учёный придумал графитовую печь, в которой при температуре 1600 — 2500 градусов Цельсия спекался углерод с кремнезёмом. В итоге получался порошок. Производитель его рекомендовал использовать как абразив. Его запустили в массовое производства. Пила, которой пользовался Муассан, как раз была с напылением из карбида кремния. Это и объясняет присутствие в исследуемом образце следов карборунда.
Заблуждение вскоре вскрылось, но камню уже было присвоено имя. Научный мир договорился: карборунд или карбид кремния называть искусственный материал, а муассанит натуральный. Настоящие образцы муассанита были обнаружены через десят лет после исследования Муассана. Это оказались неприметные тёмно-зелёные камни.
Ачесон — первый учёный, запатентовавший вещество. Успешные опыты по производству SiC до него. Первое упоминание относится к 1880 году, что на 13 лет раньше.
Экономические показатели SiC
Ключом к широкому использованию SiC является поиск экономически эффективной технологии производства монокристаллических структур, которая решит проблему «дипольной деградации» и позволит производить пластины с оптимальными размерами для массового производства. Кремниевые чипы производятся в «условно бездефектных» пластинах (не более 10% дефектных чипов) диаметром 150-200 мм при удельной стоимости 0,1 €/см2. Плотность дефектов и, соответственно, стоимость 76- и 100-миллиметровых SiC-подложек еще на порядок выше. Это связано с меньшим количеством кристаллов, большей плотностью дефектов и необходимостью адаптации стандартных процессов к нестандартным размерам подложек.
Благодаря использованию 150-миллиметровых SiC-подложек производственные затраты могут быть снижены более чем на 50 %, а необходимость в адаптации технологического процесса отпадает. Это важный шаг на пути к решению проблемы конкурентоспособности SiC-устройств, по крайней мере, для определенных применений.
Кристаллы SiC при прочих равных условиях могут иметь меньшую площадь, то есть более высокую плотность тока, и, следовательно, на платах SiC можно разместить больше чипов. Очевидно, что с увеличением плотности кристаллов затраты на производство также должны снижаться. Менее очевидным является тот факт, что связь между стоимостью подложки и стоимостью изготовления модуля не связана напрямую с размером кристалла. В общем случае фиксированного диаметра пластины ее стоимость (Waf_$) вместе с затратами на производство и тестирование (Fab_$) определяют общую стоимость. Согласно законам хорошей производственной экономики, общая стоимость должна быть пропорциональна количеству чипов на пластине NЧипдолжна быть константой:
(Waf_$ + Fab_$)/NЧип= константа.
Если цена пластины увеличивается, стоимость Fab_$ обычно не меняется, но стоимость производства модулей с кристаллами SiC увеличивается. Одним из возможных решений является переход на более крупные чипы.
Химические свойства
Схема атома кремния
В соединениях кремний склонен проявлять степень окисления +4 или −4, так как для атома кремния более характерно состояние sp³-гибридизации орбиталей. Поэтому во всех соединениях, кроме оксида кремния (II) SiO, кремний четырёхвалентен.
Химически кремний малоактивен. При комнатной температуре реагирует только с газообразным фтором, при этом образуется летучий тетрафторид кремния SiF4. При нагревании до температуры 400—500°C кремний реагирует с кислородом с образованием диоксида SiO2, с хлором, бромом и иодом — с образованием соответствующих легко летучих тетрагалогенидов SiHal4.
С водородом кремний непосредственно не реагирует, соединения кремния с водородом — силаны с общей формулой SinH2n+2 — получают косвенным путем. Моносилан SiH4 (его часто называют просто силаном) выделяется при взаимодействии силицидов металлов с растворами кислот, например:
Образующийся в этой реакции силан SiH4 содержит примесь и других силанов, в частности, дисилана Si2H6 и трисилана Si3H8, в которых имеется цепочка из атомов кремния, связанных между собой одинарными связями (—Si—Si—Si—).
С азотом кремний при температуре около 1000 °C образует нитрид Si3N4, с бором — термически и химически стойкие бориды SiB3, SiB6 и SiB12. Соединение кремния и его ближайшего аналога по таблице Менделеева — углерода — карбид кремния SiС (карборунд) характеризуется высокой твердостью и низкой химической активностью. Карборунд широко используется как абразивный материал.
При нагревании кремния с металлами возникают силициды. Силициды можно подразделить на две группы: ионно-ковалентные (силициды щелочных, щелочноземельных металлов и магния типа Ca2Si, Mg2Si и др.) и металлоподобные (силициды переходных металлов). Силициды активных металлов разлагаются под действием кислот, силициды переходных металлов химически стойки и под действием кислот не разлагаются. Металлоподобные силициды имеют высокие температуры плавления (до 2000 °C). Наиболее часто образуются металлоподобные силициды составов MeSi, Me3Si2, Me2Si3, Me5Si3 и MeSi2. Металлоподобные силициды химически инертны, устойчивы к действию кислорода даже при высоких температурах.
При восстановлении SiO2 кремнием при высоких температурах образуется оксид кремния (II) SiO.
Для кремния характерно образование кремнийорганических соединений, в которых атомы кремния соединены в длинные цепочки за счет мостиковых атомов кислорода —О—, а к каждому атому кремния, кроме двух атомов О, присоединены еще два органических радикала R1 и R2 = CH3, C2H5, C6H5, CH2CH2CF3 и др.
Карборунд
Карборунд = синтетический муассанит – искусственно полученный карбид кремния. Минералом не является
Карборунд = синтетический муассанит – искусственно полученный карбид кремния. Минералом не является.
Получают при сплавлении песка и угля (т. е. кремнезема и углерода). Напоминает антрацит, но переливается всеми цветами радуги.
Коэффициент приломления у ювелирного образца карборунда (2,65) выше чем у алмаза (2,42).
Запатентован карборунд Эдвардом Гудричем Ачесоном 28 февраля 1893, но сообщения о получении данного соединения были и раньше, например Деспретз (1849), Марсден (1880) и Колсон (1882).
Перспективы
Приведенное выше сравнение SiC-пластин в настоящее время и в 2000 г. показывает увеличение диаметра от 35 до 150 мм, достигнутое за прошедшие годы. Мы можем видеть, что качество поверхности современных пластин увеличилось в 18 раз
Постоянный рост размеров, сопровождаемый совершенствованием качества, будет оставаться наиболее важной целью и в будущем. Преимуществом больших пластин являются лучшие экономические показатели и меньшие затраты на производство
Переход от 100-мм к 150-мм пластинам для заказчиков только начинается, поэтому большой интерес вызывает возможное появление 200-мм подложек как очередной этап эволюции. Хотя для следующего шага потребуется некоторое время, чтобы сделать его коммерчески привлекательным, SiCrystal надеется, что сможет представить первые образцы в течение двух-трех лет. Предварительная работа по изготовлению 200-мм пластин уже ведется.
Свойства и описание камня карборунд
Карборунд, или муассанит – это камень, относящийся к классу полупроводникового бинарного химического соединения. Это карбид кремния, получаемый в искусственных условиях в течение 30-40 часов. Камень получают в результате плавления угля и песка. Характерен выраженный блеск, который есть у антрацита. Если камень попадает под прямые лучи солнца, он переливается всеми цветами радуги. Благодаря высокому показателю твердости (9,1 балла по шкале Мооса), карборунд может поцарапать любой минерал, кроме алмаза.
Это тугоплавкий самоцвет, характеризующийся устойчивостью к воздействию кислот и других агрессивных факторов. Не плавится при температуре свыше 1500 градусов по Цельсию. Также есть свойство преломлять свет. Выделают более 250 кристаллических форм карборунда, от которых зависит цветовая гамма. Камень не разрушается при интенсивном и продолжительном трении.
Формула и технология получения карборунда была запатентована Эдвардом Гудричем Ачесоном в 1893 году. Однако в 1842 году аналогичное соединение химических элементов было получено ученым Деспретзом.
Природный аналог встречается крайне редко. По сей день крупные залежи карборунда не удалось найти.
Обязательно посмотрите: Что такое гидротермальный изумруд и где его используют
Изотопы и их применение
Основная статья: Изотопы кремния
Кремний состоит из стабильных изотопов 28Si (92,23 %), 29Si (4,67 %) и 30Si (3,10 %). Остальные изотопы являются радиоактивными.
Ядро 29Si (как и протон) имеет ядерный спин I = 1/2 и все шире используется в спектроскопии ЯМР. 31Si, образующийся при действии нейтронов на 30Si, имеет период полураспада равный 2,62 ч. Его можно определить по характеристическому β-излучению, и он очень удобен для количественного определения кремния методом нейтронно-активационного анализа. Радиоактивный нуклид 32Si имеет самый большой период полураспада (~170 лет) и является мягким (низкоэнергетическим) β-излучателем.
Дефекты структуры SiC и характеристики модулей
Последние достижения SiC-технологии привели к значительному сокращению плотности дефектов. Как правило, качество новых и более крупных подложек всегда ниже, чем у приборов предыдущих поколений, но оно постепенно растет по мере освоения производства. Выпуск пластин диаметром 150 мм дает возможность снизить стоимость модулей, однако они все еще остаются достаточно дорогими для массового применения.
Чтобы в полной мере реализовать преимущества 150-мм SiC-подложек, их следует адаптировать для массового изготовления. Уменьшение плотности дефектов позволит обеспечить плавный переход от производства пластин меньшего диаметра к технологии 150 мм. Кроме этого, качество эпитаксиальных пленок и уровень технологических процессов должны обеспечить равномерные характеристики по всей поверхности пластины.
Наиболее известными «врагами» карбида кремния являются так называемые микротрубки или микропоры, представляющие собой кристаллографические дефекты структуры. С тех пор как компания Dow Corning разработала свою технологию 150-мм пластин, плотность микропор поддерживается на уровне менее 1/см2.
В процессе производства материал подложки подвергается воздействию внутренних и внешних стрессов, что приводит к увеличению размера дефектов и сдвигам внутри атомной решетки. Чаще всего возникает так называемое «винтовое смещение», которое нарушает последовательность атомных плоскостей в кристаллической решетке и располагает их в форме спирали. Винтовое смещение, происходящее во время выращивания подложки, образует микропоры, с повышением плотности которых резко растет процент дефектных чипов. Технология Dow Corning обеспечивает не только низкую плотность микропор в пластинах диаметром до 150 мм, но и сверхмалый уровень винтовых и базальных (плоскостных) смещений.
На рис. 1 в хронологическом порядке показано снижение количества микропор в 4H SiC-пластинах, полученное за счет внедрения технологии PVT Dow Corning. Это позволило довести среднее значение плотности дефектов до <0,1/см2. Подробные замеры винтовых смещений на пластинах 76 мм показали очень хорошие результаты, их статистическое распределение в группе кристаллов приведено на рис. 2.
Рис. 1. Средняя плотность микропор в пластинах 4H SiC диаметром 76 и 100 мм (производство с ноября 2009 по январь 2011 г.)
Рис. 2. Измерения плотности винтовых смещений на 25 кристаллах нескольких 4H SiC-пластин. Анализ проводился методом рентгеновской топографии по девяти участкам на пластине (каждый столбец отображает девять точек измерений). Группы представляют собой две выборки выпускаемой продукции за период с середины 2009 по середину 2010 г.
Степень выхода годных SiC ограничена в основном поверхностными дефектами, образующимися при химическом осаждении из газовой фазы в ходе эпитаксиального процесса (CVD). На сегодня это наиболее значимая проблема, резко снижающая эффективность работы полупроводниковых устройств. Размеры эпитаксиальных дефектов зависят от толщины пленки, а их плотность (1,5–2/см2) характерна для приборов с блокирующим напряжением ниже 2 кВ. Для решения этой проблемы и адаптации 150-мм пластин к серийному производству была разработана эпитаксиальная технология, обеспечивающая приемлемую плотность эпитаксиальных дефектов на подложках разного диаметра. Новая технология пригодна для использования легирующих примесей n— и p-типа, она также допускает увеличение толщины слоя эпитаксии свыше 50 мкм для высоковольтных приложений.
Компания Dow Corning разработала и внедрила процесс эпитаксии CVD для производства 4H SiC-подложек толщиной до 100 мкм. Очень важным критерием качества пленок является количество дефектов, добавляемых в процессе формирования эпитаксиального слоя. При крайне низком уровне MPD в современных 4Н SiC-пластинах дефекты эпитаксии, скорее всего, в наибольшей степени влияют на выход годных в процессе изготовления. Их влияние оценивается путем лазерной светорассеивающей спектрометрии. Пластина разделяется на области, каждая из которых исследуется с помощью лазерного сканирующего спектрометра. Зоны, содержащие дефекты, помечаются как бракованные, плотность дефектов определяется с помощью распределения Пуассона. На рис. 3 показана общая плотность дефектов (пластин и эпитаксии) для подложек Dow Corning диаметром 76 мм, полученная в течение пяти кварталов непрерывного производства.
Рис. 3. Распределение общего количества дефектов (подложки и эпитаксии) для пластин 76 мм, измерения проведены методом лазерной светорассеивающей спектрометрии
Открытие и начало производства[ | ]
Повторение эксперимента Г. Д. Раунда
О ранних, не систематических и часто непризнанных синтезах карбида кремния сообщали Деспретз (1849), Марсден (1880) и Колсон (1882 год). Широкомасштабное производство начал Эдвард Гудрич Ачесон в 1893. Он запатентовал метод получения порошкообразного карбида кремния 28 февраля 1893. Ачесон также разработал электрическую печь, в которой карбид кремния создаётся до сих пор.
Исторически первым способом использования карбида кремния было использование в качестве абразива. За этим последовало применение и в электронных устройствах. В начале XX века карбид кремния использовался в качестве детектора в первых радиоприемниках. В 1907 году Генри Джозеф Раунд создал первый светодиод, подавая напряжение на кристаллы SiC и наблюдая за жёлтым, зелёным и оранжевым излучением на катоде. Эти эксперименты были повторены О. В. Лосевым в СССР в 1923 году.
Синтетические кристаллы SiC ~ 3 мм в диаметре
Чистота карбида кремния, образующегося в печи Ачесона, зависит от расстояния до графитовогорезистора в ТЭНе.
Чистый карбид кремния можно получить с помощью так называемого процесса Лели, в котором порошкообразный SiC возгоняется в атмосфере аргона при 2500 °C и осаждается на более холодной подложке в виде чешуйчатых монокристаллов размерами до 2×2 см. Этот процесс даёт высококачественные монокристаллы, получающиеся из-за быстрого нагрева до высоких температур и в основном состоящие из 6H-SiC фазы.
Чистый карбид кремния также может быть получен путём термического разложения полимера полиметилсилана (SiCH3)n, в атмосфере инертного газа при низких температурах. Относительно CVD-процесса метод пиролиза более удобен, поскольку из полимера можно сформировать изделие любой формы перед запеканием в керамику.
Предлагаем ознакомиться Куб циркон что это
О компании SiCrystal AG
SiCrystal AG, один из ведущих мировых производителей полупроводниковых SiC-подложек, основана в 1996 г. со штаб-квартирой в г. Нюрнберг (Германия). SiCrystal AG является дочерней компанией ROHM Co. ltd, поставляющей свою продукцию клиентам по всему миру. SiCrystal AG владеет всеми технологическими этапами — от производства исходного материала до упаковки т. н. «эпи-полированных» (epi-ready) подложек в собственных стерильных цехах. В дополнение к фирменным методам анализа, SiCrystal AG имеет прямой доступ к результатам испытаний компонентов в пределах группы ROHM. Это является неоценимым преимуществом для дальнейшей оптимизации свойств материала, основанной на оценке производительности кристаллов и даже модулей.
Изготовление SiC-подложек: производственная цепочка
В конце процесса выращивания цилиндрический монокристалл длиной несколько сантиметров, диаметр которого несколько превышает заданное значение, может быть изъят из тигля. Последующие производственные этапы почти идентичны для других полупроводников, в частности кремния:
- ориентация кристаллов с помощью рентгеновского анализа;
- цилиндрическое шлифование кристалла до нужного диаметра;
- шлифование поверхностей (маркировка на поверхности кристалла);
- распиливание пластин;
- применение индивидуальной лазерной маркировки для идентификации пластин;
- закругление кромок пластин;
- обработка поверхностей с использованием следующих методов:
- шлифование;
- притирка;
- полирование путем механического истирания;
- полирование путем химического/механического истирания;
- очистка пластин с помощью сухих или влажных химических методов.
Разумеется, все описанные этапы сопровождаются проверкой многих внутренне или внешне заданных параметров с использованием специальных оптических, механических, химических и электрических методов. Большой объем полученных и архивированных данных обеспечивает полную «отслеживаемость» производства конечной продукции, от исходного сырья, используемого в начальной стадии.
Описанная выше технология давно зарекомендовала себя в качестве стандарта в изготовлении полупроводниковых подложек. Технологические этапы, оборудование и методы контроля, в основном, известны по производству кремния. Тем не менее некоторые процессы и/или оснастку приходилось изменять, чтобы учесть специфические свойства SiC, который является очень твердым материалом. По шкале твердости Мооса, где алмазы находятся на верхнем пределе с твердостью 10, а минералы считаются очень жесткими, если их твердость выше 6, SiC (твердость 9) — один из лидеров. Всего несколько материалов являются пригодными для абразивной обработки SiC. Инструменты и даже технологическое оборудование должны быть адаптированы для обеспечения необходимой точности обработки.
Из космоса и из печки
Карбид кремния, карборунд, муассанит – все это названия одного химического соединения. Различия − в его родословной. Муассанитом принято называть карбид кремния органического происхождения, а карборунд – это торговое и техническое название соединения.
Муассанит получил свое наименование в честь первооткрывателя − Анри Муассана, французского химика, нобелевского лауреата. В 1893 году, изучая фрагменты метеорита, он обнаружил мельчайшие частицы нового минерала, который и назвали его именем. Нужно сказать, что в природной форме на нашей планете муассанит встречается крайне редко и в незначительных объемах. Зато его без проблем можно найти в огромных количествах в пылевых космических облаках, особенно за пределами Солнечной системы.
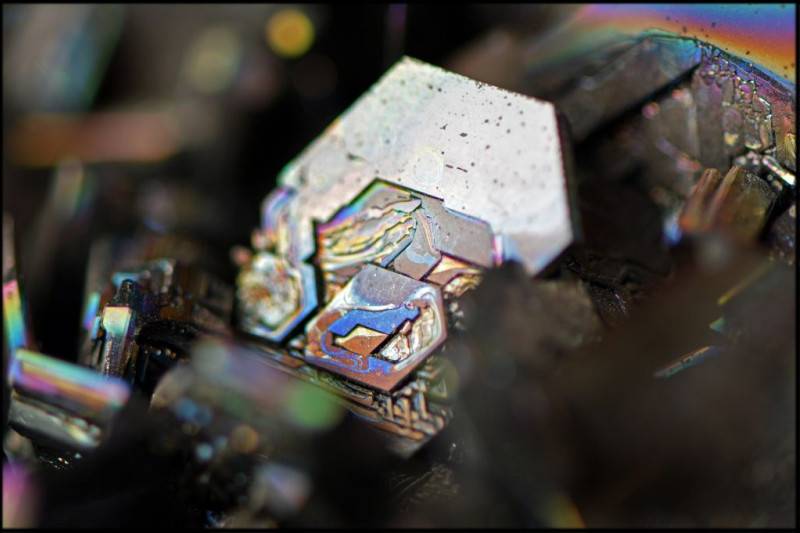
Кристалл карбида кремния. Фото: Lamiot / wikimedia.org
По удивительному совпадению получить карбид кремния искусственным методом удалось в том же 1893 году. Американец Эдвар Ачесон не только изобрел процесс синтеза вещества, но и придумал для этого электрическую печь, которая до сих пор применяется и носит имя своего создателя.
Основными сырьевыми компонентами для карборунда являются кварцевый песок и кокс. Спекание составляющих происходит в печи Ачесона при температуре от 1600 до 2500 градусов. Высококачественные чистые кристаллы можно получить в ходе процесса Лели путем возгонки порошка карбида кремния, то есть перевода его в парообразное состояние, и последующего осаждения.
Вещество, получившее химическую формулу SiC, обладает уникальными свойствами. Карбид кремния – это сверхтвердый кристалл с очень высокой термической, химической и радиационной стойкостью. Его невозможно расплавить даже при очень высоком давлении. При обычных температурах карборунд практически не вступает в реакцию с другими веществами.
Современность
В конце XX был изготовлен первый кристалл карборунда, до этого он был известен только в виде порошка. Как только появилась возможность синтезировать кристалл – его синтезировали. Результат оказался поразительным. По многим показателям карборунд превосходил алмаз.
- степень светопреломления на четверть выше;
- дисперсия – в два с половиной.
То есть он лучше блестит и даёт больше радужных бликов. Казалось бы – вот она, удача. Его действительно признали лучшей имитацией алмаза. Но в массовым он так и не стал. Делать ювелирные изделия с карборудном с точки зрения коммерции бессмысленно.
Производство украшений из камня слишком сложное и затратное дело. Крупный образец будет стоить порядка 500 долларов за карат. Сомнительно, что найдутся любители покупать искусственные камни за такие деньги. Даже если они высокотехнологичные и сверхблестящие. Сейчас кристаллы карбида кремния делает только одна американская компания, а в продаже он встречается реже, чем бриллиант.
Теоретически камень должен быть красивым: блестящий, сияющий, с радужной игрой света на гранях.
Но ценители камня его не очень ценят. На то есть несколько причин:
- яркие переливы света непривычны глазу и скорее раздражают, создают впечатление безвкусности и кичливости;
- прозрачных и чистых по цвету камней нет. Все они имеют пыльный зеленоватый оттенок. Химики пока с этим ничего поделать не могут;
- лучики света, которые отбрасывает бриллиант плотные, яркие, с насыщенными оттенка. Карборунд даёт более прозрачные и тёмные отблески.
Как видим, искусственному муассаниту не удалось превзойти алмаз и вытеснить его с ювелирных прилавков.
Непрозрачные недорогие образцы предприимчивые итальянцы продают как куски лавы Везувия.
Однако у карборунда есть ряд преимуществ:
- он не оставляет на себе жировых отпечатков. Если долго щупать бриллиант, он покроется жировой плёнкой и блестеть перестанет. Карборунд к этому невосприимчив. сколько его не трогай – он продолжит блестеть;
- поскольку карборунд выращен искусственно, он лишён дефектов. Его ограняют в идеальные, математически точно выверенные кристаллы. К тому же на материале можно не экономить. С бриллиантами это не всегда проходит. Иногда хочет сохранить вес камня и умышленно нарушает пропорции, иногда обходит дефекты. Браком это не считаются. Такие бриллианты хоть и стоят ниже, но на рынок поступают;
- в экстремальных температурах (около 1000 градусов Цельсия) алмаз горит, а карборунд нет. Вы можете кинуть платиновое кольцо в угольную печь и оно не пострадает.
Кроме этого он прочный, лишь незначительно уступает алмазу. К тому же он инертный – не вступает в реакцию с другими веществами (кроме плавиковой, азотной и ортофосфорной кислот), отличается высокой теплопроводностью, плотностью электрического тока и электрическим напряжением, имеет малый коэффициент теплового расширения и не имеет фазовых переходов, разрушающих кристалл.
Сейчас карборунд производят методом термического разложения полиметилсилана при низких температурах в присутствии инертного газа. Полученный материал применяется во многих сферах жизни.
Применяется в качестве:
- абразив для шлифования и напыление для пил;
- сырьё для режущих инструментов;
- полупроводник в электротехнической промышленности;
- катализатор в химической промышленности;
- подшипники и элементы оборудования в плавильных печах, поскольку он выдерживает нагрузку до 1700 градусов Цельсия;
- сырьё для производства бронежилетов;
- основа для сверхмощных светодиодов;
- сырьё для изготовления высококачественных дисковых тормозов;
- сырьё для создания зеркальных деталей в оптических системах.
Это далеко не всё. Камень используется в ядерной энергетике, строительстве, органическом синтезе.
Естественное явление
Монокристалл муассанита (размер ≈1 мм)
Встречающийся в природе муассанит содержится в очень незначительных количествах в некоторых типах метеоритов, а также в месторождениях корунда и кимберлитах . Практически весь карбид кремния, продаваемый в мире, включая муассаниты, является синтетическим . Природный муассанит был впервые обнаружен в 1893 году как небольшой компонент метеорита Каньон Диабло в Аризоне доктором Фердинандом Анри Муассаном , в честь которого этот материал был назван в 1905 году. Открытие Муассаном природного SiC первоначально оспаривалось, поскольку его образец мог быть загрязнен лезвиями из карбида кремния , которые уже были на рынке в то время.
Карбид кремния, хоть и редко встречающийся на Земле, широко распространен в космосе. Это обычная форма звездной пыли, обнаруживаемая вокруг богатых углеродом звезд , и примеры этой звездной пыли были обнаружены в первозданном состоянии в примитивных (неизмененных) метеоритах. Карбид кремния, обнаруженный в космосе и в метеоритах, почти всегда является бета-полиморфом . Анализ зерен SiC, обнаруженных в метеорите Мерчисон , углеродистом хондритовом метеорите, выявил аномальные изотопные отношения углерода и кремния, указывающие на то, что эти зерна возникли за пределами Солнечной системы.
Ранние эксперименты
Несистематические, менее признанные и часто непроверенные синтезы карбида кремния включают:
- Сезар-Мансуэт Деспре пропускает электрический ток через угольный стержень, погруженный в песок (1849 г.)
- Растворение кремнезема в расплавленном серебре в графитовом тигле Роберта Сидни Марсдена (1881 г.)
- Нагревание смеси кремния и кремнезема в графитовом тигле Пауля Шютценбергера (1881 г.)
- Нагревание кремния Альбертом Колсоном в потоке этилена (1882 г.).
Масштабное производство
Репликация экспериментов HJ Round со светодиодами
Широкомасштабное производство приписывают Эдварду Гудричу Ачесону в 1890 году. Ачесон пытался приготовить искусственные алмазы, когда он нагрел смесь глины (силикат алюминия) и порошкообразного кокса (углерода) в железной чаше. Он назвал голубые кристаллы, которые образовали карборунд , полагая, что это новое соединение углерода и алюминия, подобное корунду . Муассан также синтезировал SiC несколькими способами, включая растворение углерода в расплавленном кремнии, плавление смеси карбида кальция и кремнезема и восстановление кремнезема углеродом в электрической печи.
Ачесон запатентовал метод производства порошка карбида кремния 28 февраля 1893 года. Ачесон также разработал электрическую печь периодического действия, с помощью которой SiC производится до сих пор, и сформировал Carborundum Company для производства объемного SiC, первоначально для использования в качестве абразива. В 1900 году компания заключила соглашение с Electric Smelting and Aluminium Company, когда решением судьи ее основатели “в целом” отдавали приоритет “восстановлению руд и других веществ методом накаливания”. Говорят, что Ачесон пытался растворить углерод в расплавленном корунде ( оксид алюминия ) и обнаружил присутствие твердых сине-черных кристаллов, которые он считал соединением углерода и корунда: отсюда и карборунд. Возможно, он назвал материал «карборунд» по аналогии с корундом, который является еще одним очень твердым веществом (9 по шкале Мооса ).
SiC впервые использовался в качестве абразива. Затем последовали электронные заявки. В начале 20 века карбид кремния использовался в качестве детектора в первых радиоприемниках. В 1907 году Генри Джозеф Раунд создал первый светодиод, подав напряжение на кристалл SiC и наблюдая желтое, зеленое и оранжевое излучение на катоде. Позднее этот эффект был открыт О.В. Лосевым в Советском Союзе в 1923 году.
Применение материала
Основной областью применения карбида кремния является электроника и энергетика. Это вещество используется при производстве полупроводниковых механизмов, светодиодов, резисторов, транзисторов и счетчиков энергии. Эти приспособления обладают высокой прочностью и могут стабильно функционировать в течение 10 лет. Они применяются в высокочастотной электронике. Изделия из карбида кремния отличаются следующими свойствами:
- Обладают большой шириной запрещенной зоны;
- Могут функционировать при высоких температурах (до 600 °C);
- Располагают повышенной теплопроводностью, в отличие от приборов, выполненных из арсенида галлия и иных минералов.
- Устойчивы к радиации и воздействию электрических зарядов.
Благодаря высокой огнеупорности и теплостойкости материала, он активно применяется в металлургии и химической промышленности. Из твердого раствора карборунда изготавливается множество нагревательных приборов, способны работать при высоких температурах (до 2000 °C). Эти приспособления могут функционировать в нейтральных или восстановленных средах. Нагревательные элементы активно используются при термообработке металлических деталей для керамических приборов и электронных компонентах.
Карбид кремния применяется в качестве абразива, что обусловлено высокой прочностью и низкой стоимостью химического соединения. При абразивной обработке этот материал используется в следующих процессах:
- шлифование;
- ламинирование бумажных изделий;
- пескоструйная обработка;
- хонингование;
- водоструйная резка.
Карборунд нашел широкое применение в производстве конструкционных материалов. Он обладает стойкостью к физическим нагрузкам и активно используется при изготовлении пуленепробиваемых жилетов и дисковых тормозов, устанавливаемых на транспортном средстве. С 1990-х гг. из карборунда изготавливают прочные газовые турбины. Они устойчивы к высоким температурам и ударным нагрузкам.
Источник